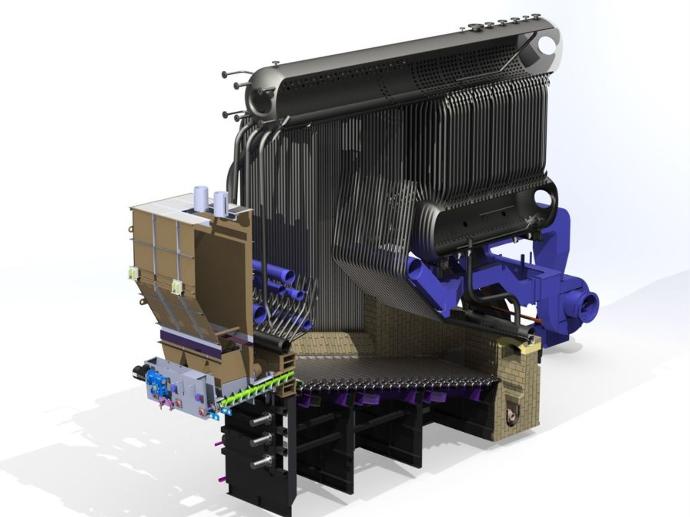
Водотрубний двобарабаний паровий котел на біомасі DBW
Двобарабанний водотрубний паровий котел DBW із природною циркуляцією та можливістю перегріву пари — це високоефективне, надійне та екологічне рішення для ваших промислових потреб. У цьому котлі, що працює на біомасі та низькосортному паливі з теплотворною здатністю не більше 5500 ккал/кг, застосовано передові технології, що забезпечують якісне спалювання палива та надійність котла.
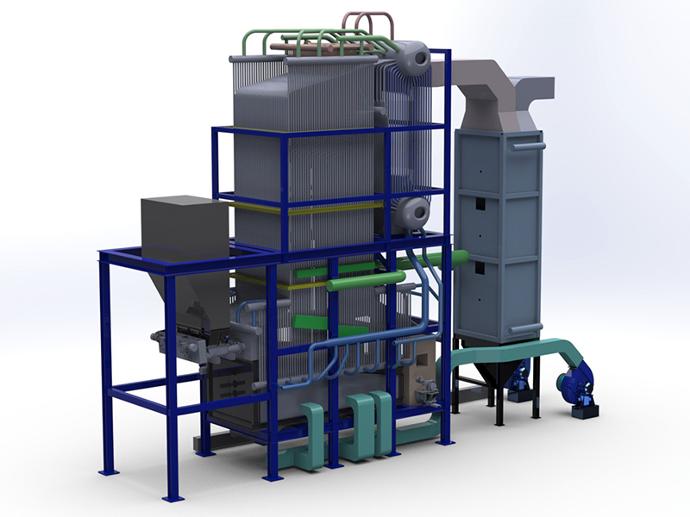
Безпечний для довкілля
Завдяки використанню біомаси та низькосортного палива наш котел не тільки ефективний, але й екологічно чистий. Це сприяє розвитку зеленої енергії та дозволяє використовувати сільськогосподарські відходи як паливо.
Конструкція парового котла дозволяє спалювати наступні види палива, але ми не обмежуємося цими варіантами. Цей список можна розширити, і він далеко не вичерпний:
- Лушпиння соняшника
- Відходи птахофабрик
- Соломка з вівса та інших злаків
- Торф
- Лігнін
- Стебла кукурудзи
- Паливні пелети